The ensuing cladding layer was properly bonded, and the blades exhibited improved fatigue characteristics in contrast with blades shaped by the conventional silver brazing process. laser beam. The alloy was overlaid on the steel as a powder layer 2.5 mm thick. After melting and bonding by the laser, the alloy layer was 1.5 mm thick and had little or no dilution from the metal. The resulting floor had wonderful wear resistance.
Its business identify is Zircaloy, or Zry for short. Zry is available in two varieties, Zry-2 and Zry-4. These two differ by minor changes within the concentrations of the transition metals (Zry-4 has no nickel). PWRs use Zry-4 whereas BWRs make use of Zry-2 as cladding and both Zry-2 or Zry-four for the duct or channel holding the fuel-component bundle.
The constants a and b are fundamental properties of the material and may be determined from standard laboratory experiments on fresh fuel. In explosive welding, a compression force created by detonation of explosives is used to hitch overlapping metallic sheets. The becoming a member of elements are arranged in the direction of one another at an angle of 1–15°, depending on the material and methodology, and are ready with a layer of explosive on the highest. After ignition the becoming a member of areas are moved against each other at high velocity.
tube. Energy, from fission, is generated roughly uniformly throughout the fuel pellets. Heat is extracted on the rod surface by the coolant move. The temperature at the hottest level, on the pellet centerline, is usually within the vary 800–one thousand °C, depending on the power degree. The metallic cladding is a good conductor, so the temperature rise throughout the wall is just a few tens of levels.
In one, a second inside-surface liner of odd Zry is extruded on the sponge zirconium liner in order to restore corrosion resistance. In other modifications, the sponge zirconium is alloyed with iron or tin to enhance oxidation resistance without affecting the softness that provides immunity from PCI. Standard Zry is sufficiently hard to be susceptible to stress-corrosion cracking (SCC) when the pellet–cladding hole closes and the swelling gas generates substantial tensile hoop stresses within the cladding. In the presence of an aggressive fission product (iodine is most often cited), a brittle crack may be initiated and penetrate the cladding wall.
In our cladding options we think about the styling and hues, selection of supplies, lighting design and overall setting of the building as key CI components, so that every little thing matches your individual necessities. Although the thermal properties of façade coverings used to be of primary significance, today company id (CI) elements are essential to the design of the panels. ACM (aluminium composite), glass, pure stone and sheet metal are just some of the supplies that can be used in the big variety of plate-holders and sections. , the place T is the absolute temperature and β is the burnup.
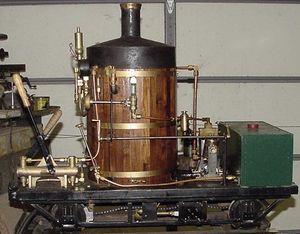
cladding

Zry production strategies now offer much better management of gaseous impurities than early fabrication expertise, so the original purpose for adding tin is moot. Since tin is a substitutional impurity, its function is to extend the power of Zry over that of pure zirconium. 1.5% tin, and the stability being iron, nickel, and chromium.
The thickness of the cladding is a design parameter dictated by conflicting performance requirements. The impact of loss of steel by internal or outer corrosion is much less important for thick cladding than for skinny-walled tubing.
Increased wear and oxidation resistance of titanium aluminide alloys by laser cladding Euro Superalloys. Increased put on and oxidation resistance of titanium aluminide alloys by laser cladding. A structured separating layer, consisting of a 3-layer vapour-permeable roof underlay membrane with self-adhesive butyl strips, bonded to monofilaments organized in a random community, to be used as a spacer layer between the roof construction and the steel cladding. Those areas subjected to excessive warmth - from the exhaust manifold or catalytic converter for instance - could be insulated by a refractory materials and metallic cladding. Wire-based mostly laser deposition welding is a material-environment friendly 3D printing course of for the manufacturing of metallic components.
Enhance the curb appeal of your own home with B&Q cladding. All of our timber is responsibly sourced forest pleasant timber.
The buildup of those can be suppressed by adding hydrogen in the coolant water. Dissolved hydrogen focus in PWR coolant is maintained at a level of two.2–four.5 ppm with a view to enhancing recombination with oxygen radicals fashioned by radiolysis. The PHWR coolant doesn't include boric acid and deuterium is added in place of hydrogen.
Aluminum Cladding
Today, Zircaloy-2 and Zircaloy-four are widely used. Phase transformation of Zirconia is, however, of nice concern.
This is a major cladding failure that admits steam into the rod with the accompanying potential for a more severe secondary failure because of hydriding. The mixture of situations (prone steel, tensile stress, and chemical enhancer) that produces the first defect is termed pellet–cladding interaction (PCI). scale that grows round them during in-reactor operation. This loss of the insulating properties of the oxide is believed to speed up the corrosion price.
The transition metals iron and chromium appear in the microstructure as precipitates of the intermetallic compounds Zr 2 (Ni,Fe) and Zr(Cr,Fe) 2 . These minor alloying elements improve corrosion resistance to an extent dependent on the size of the precipitates. Laser cladding has been utilized to hardening of steam generator turbine blades and reached pilot production standing [4 ]. The blades had a machined pocket, into which powdered cobalt-based metal (Stellite 6) was fed ahead of the laser beam.
The helium filling fuel can also be a reasonably good conductor, however solely as long as it stays uncontaminated by fission products. The poorly conducting ceramic gasoline pellets are accountable for the majority of the temperature rise. The evolution of the conductivities of the pellet and filling gasoline determine how the thermal efficiency develops with burnup.
The complete melting of the filler ends in a dense layer with optimal adhesion to the substrate. The most typical utility is for the wear and tear safety, e.g. of tools, but in addition corrosion protection or excessive temperature resistance may be specifically improved. Common exhausting alloys based on cobalt, nickel and iron are used with and without the addition of onerous materials. But additionally specifically tailored supplies can be applied.
The thickness of the cladding is a design parameter dictated by conflicting performance requirements. The impact of loss of metal by inner or outer corrosion is much less important for thick cladding than for thin-walled tubing.
Once the pellet/clad gap is closed, any change in pellet dimensions causes stress in the cladding and the synergy between the stress and the corroding medium induces the SCC process. In order to prevent or decrease pellet/clad interactions, each mechanical and chemical, a coating of graphite powder is applied on the inside surface of cladding tubes.
Its business identify is Zircaloy, or Zry for short. Zry is available in two varieties, Zry-2 and Zry-4. These two differ by minor changes within the concentrations of the transition metals (Zry-four has no nickel). PWRs use Zry-four whereas BWRs employ Zry-2 as cladding and both Zry-2 or Zry-4 for the duct or channel holding the gas-factor bundle.
The melt layer is kind of skinny; for example, when cladding an aluminum alloy it is about zero.5–4μm (Kreye 1985, 1997 ). The dilution of the molten zones results in airplane or corrugated interfaces. During mechanical decladding, the gas assemblies are chopped and the gas core is leached with nitric acid, leaving behind the undissolved cladding materials for disposal as a solid waste.
In our cladding solutions we consider the styling and colors, alternative of supplies, lighting design and total setting of the constructing as key CI elements, so that every little thing matches your particular person necessities. Although the thermal properties of façade coverings used to be of major importance, today corporate identity (CI) elements are crucial to the design of the panels. ACM (aluminium composite), glass, natural stone and sheet metallic are just a number of the materials that can be utilized in the big variety of plate-holders and sections. , where T is the absolute temperature and β is the burnup.
Joining happens repeatedly by local plastic deformation of the contact space (Ruge 1993 ) (see Fig. 1 ). Figure 6 . Schematic diagram showing the mechanism of the oxidation course of and the oxide movie structure on zircaloy. Figure 5 .
The oxidation course of and the nature of the oxide layer on a zirconium alloy pattern are schematically illustrated in Fig. 6 . Cladding is an outer layer of both vertical or horizontal materials, used to improve the appearance, thermal insulation and the climate resistance of a building. Our cladding is out there in a wide range of sizes, kinds of timber and floor finishes.

D. visit homepage Laser find out hereRead Full Report Cladding

The filler materials can either be provided in powder form e.g. as metal powder, or with a welding wire. When laser cladding is carried out utilizing powder, the laser normally heats the workpiece with a defocussed laser beam and melts it domestically. At the identical time, an inert gasoline mixed with a nice metal powder is launched. The metallic powder melts at the heated area and is fused to the floor of the workpiece.
In PWRs the closure of the hole between the pellet and the clad takes about one full energy year whereas the gap is maintained for a longer interval in BWRs. Due to the collapsible clad design of PHWRs, contact between the pellet and the clad is established proper from the start of the lifetime of the fuel component. Laser coating or laser cladding can be used to regionally functionalize metallic parts. In this process, an edge layer of typically 0.1 to 2 mm is applied to the part. The coating materials employed is both powder or wire, or utilized prematurely as a tape.
The thickness of the cladding could vary between zero.1 and 30 mm and the detonation velocity is between 1200 and 7000 ms −1 . The top plate hits the underside plate with a pace of one hundred–a thousand ms −1 , and pressures are in the vary of 10 to a hundred kbar. Under sure circumstances a superheated layer of material types in the contact area. The joint is then caused by a deformation-induced melting bathtub.
Hydrogen addition in boiling water circumstances is not very effective due to the segregation of hydrogen within the steam part. The interplay that gas cladding tubes expertise because of the fission products on the internal surface is stress corrosion cracking (SCC). Iodine, caesium, and cadmium are a few of the fission products which contribute strongly to the SCC process. Due to the combined results of thermal growth of gas pellets, gasoline swelling due to fission fuel launch, and the coolant strain on the outer surface of fuel tubes, cladding tubes collapse on the gasoline pellets.
The melt layer is quite skinny; for example, when cladding an aluminum alloy it's about 0.5–4μm (Kreye 1985, 1997 ). The dilution of the molten zones results in plane or corrugated interfaces. During mechanical decladding, the fuel assemblies are chopped and the gasoline core is leached with nitric acid, leaving behind the undissolved cladding material for disposal as a solid waste.